
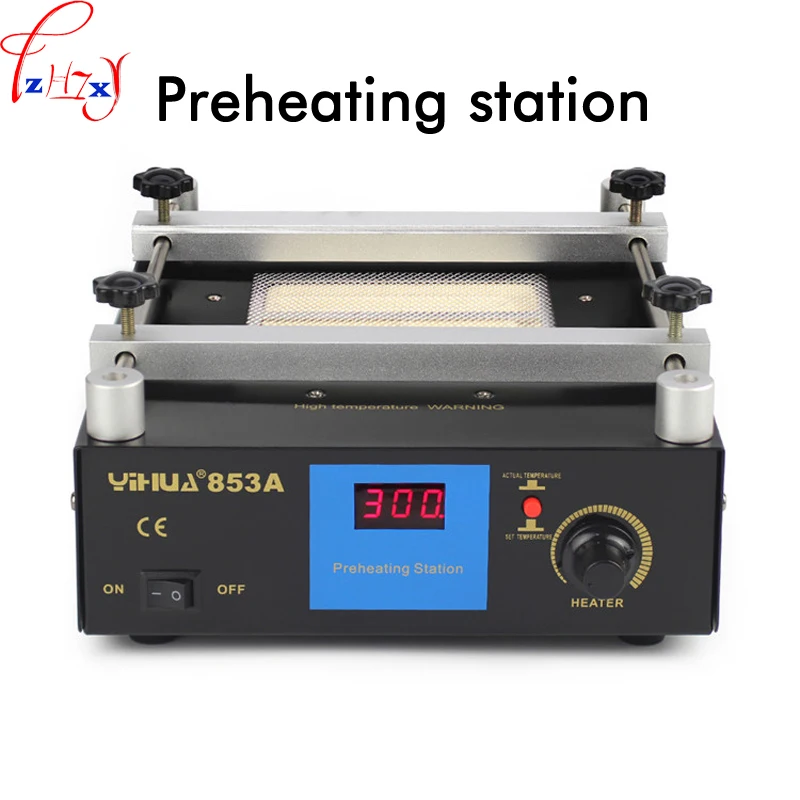
A reflow oven is typically required to mount or remove a BGA component to or from a board.

This is true even if there are only one or two BGA components on a board, or only one or two boards to be built, due to the advanced equipment required to reliably mount BGA components. Typically, boards with BGAs must be sent out to a manufacturing house to mount the BGA components. With BGA components, it is not possible to mount, remove or rework a part board with the conventional soldering iron and heat gun located in most nonproduction, basic maintenance-only labs. Since a mounted BGA component's solder joints are inaccessible beneath the package body, it is difficult to make modifications to the design. Harding, in Rapid System Prototyping with FPGAs, 2006 6.3.2 Mounting and Reworking BGA ComponentsĪ significant challenge related to BGA components is the limited number of rework options. The failure mechanisms were cracks and delamination at the solder mask/copper trace interface as shown in Fig. 5.5.3. As such, 27 and 35 mm PBGA degraded one and two MSLs, respectively. The 35 mm PBGA performed worse at the lead-free reflow temperature. However, 27 mm PBGA failed at MSL 2a and passed MSL 3 at the lead-free reflow temperature (260☌). It was found that 27 and 35 mm PBGA both can pass MSL 2a at the normal reflow temperature (maximum 225☌). In this table, a floor life at 30☌/60% RH conditions is assumed with a life of 1 year at MSL 2, 1 month at MSL 2a, 1 week at MSL 3, and 3 days at MSL 4. The detailed MSL assessment results were shown in Table 5.5.1. For each MSL level assessment, a new set of packages are used. The assessment flow chart is shown in Fig. 5.5.2. Fig. 5.5.1 shows the schematic of the BGA under consideration. Here a 27 mm PBGA with two-layer substrate and 35 mm PBGA with four-layer substrate combined with nongreen mold compound and die attach paste (silver filled epoxy) was used to assess the impact of reflow temperature (maximum 260☌) on MSL performance. Figure 8.7 illustrates the different described BGA packages. Accordingly, their classification is briefly described next. However, the most convenient way of classifying BGA packages is based on the type of material of the chip-carrier substrate.
BGA REFLOW TEMPERATURE FULL
Based on the array of solder joints, BGAs can be classified as peripheral array, staggered array, depopulated array, or a full area array. BGA packages truly reflect the advantages and disadvantages of area array interconnection mentioned previously.īGAs are classified in a number of different ways.

It is also referred to as face-bonding or controlled collapse soldering. Conventional BGA technology emphasizes soldering directly between the chip carrier package and the interconnect substrate. Prashant Chouta, in Fiber Optic Data Communication, 2002 8.1.5.1 Ball Grid Array PackagesīGA packages are rapidly gaining acceptance in the electronics industry as a low-cost, higher yielding alternative to fine pitch leaded packages.
